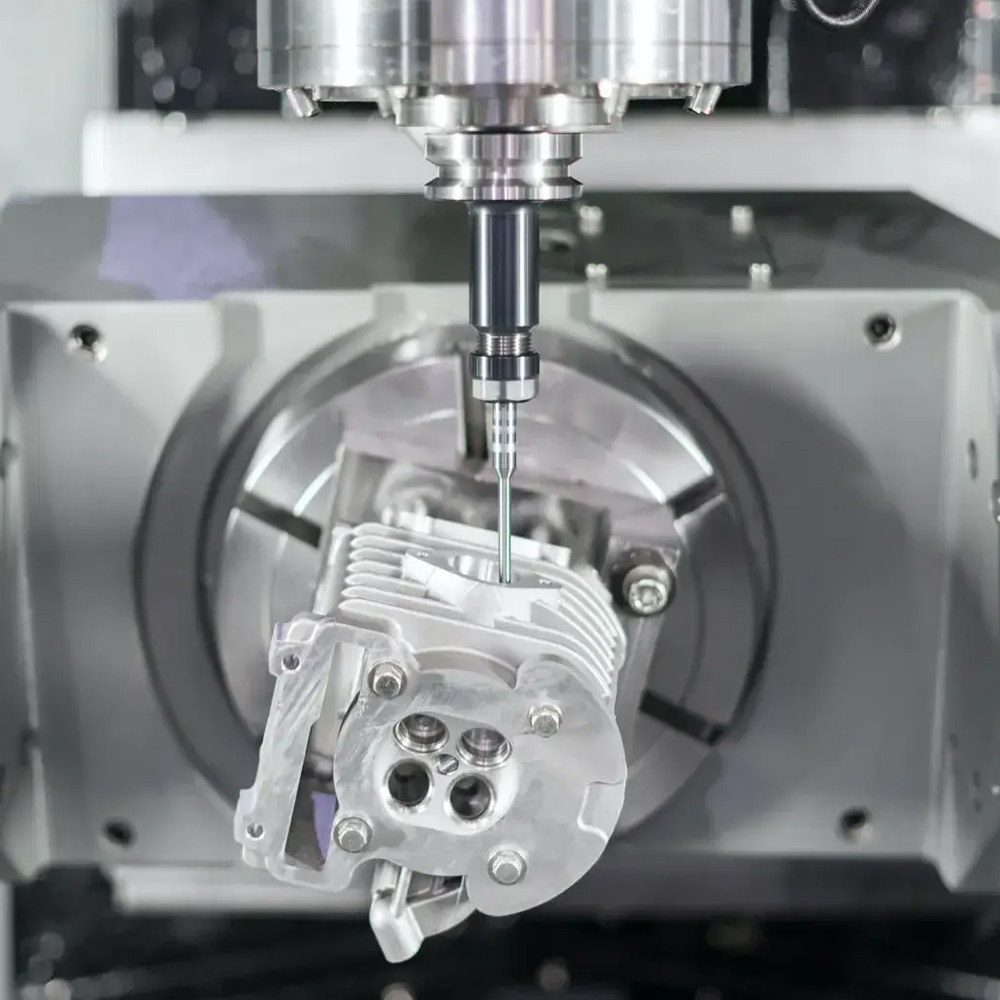
Unlocking Precision and Versatility: Exploring CNC Machining Applications and Advantages
In today’s manufacturing landscape, CNC machining stands as a cornerstone of precision and versatility. From aerospace engineering to consumer electronics, the realm of CNC machining spans industries, shaping the production of countless products. This article delves into the myriad advantages and applications of CNC machining, shedding light on its indispensable role in modern manufacturing.