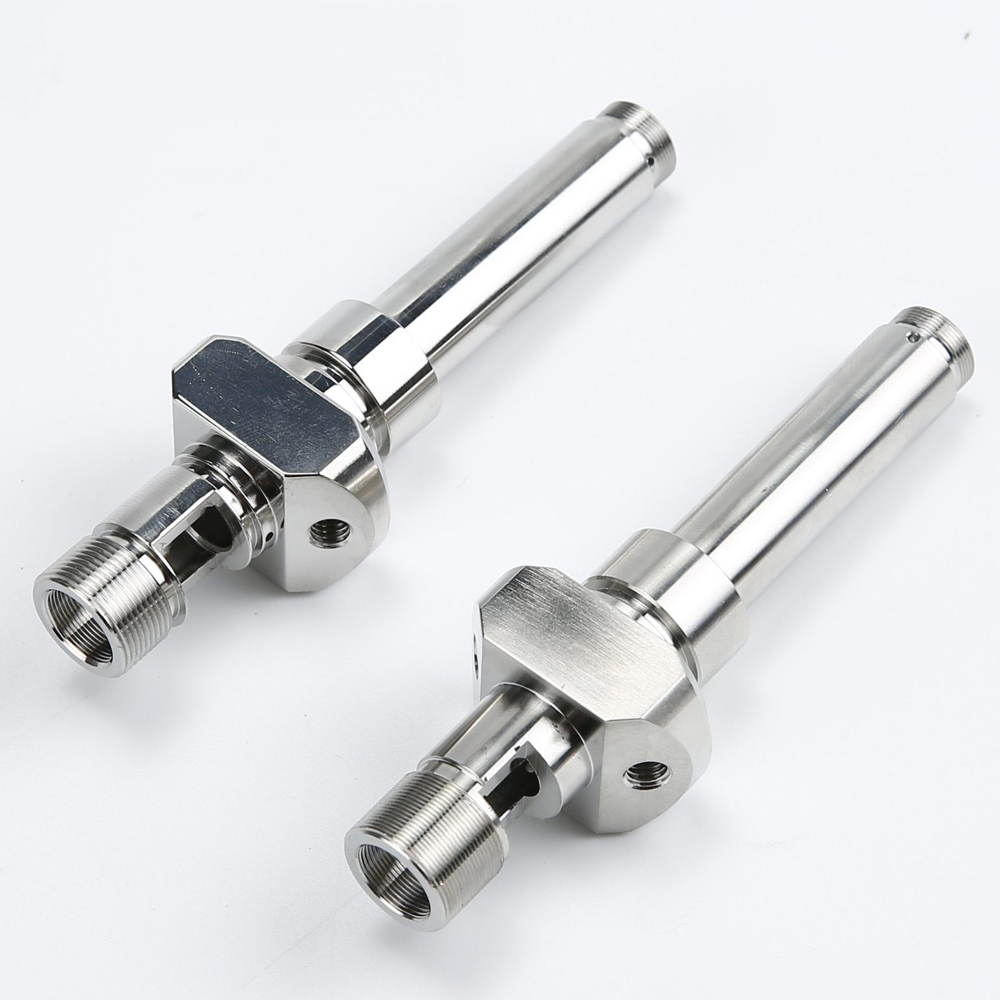
In today’s era of technological prowess, Computer Numerical Control (CNC) has revolutionized manufacturing. This ingenious method employs preprogrammed software to orchestrate the movements of machine tools with unparalleled precision and efficiency.
CNC machining encompasses various types of machines, each tailored to specific manufacturing needs. From the versatile CNC milling machines to CNC lathe machines, routers, 3D printers, and laser cutters, these tools empower industries with their diverse capabilities.
CNC Milling Parts machines stand out as indispensable tools across numerous industries. With a plethora of brands and configurations available, these machines boast diverse functionalities tailored to workshop requirements.
Every CNC milling machine comprises fundamental components essential for its operation:
1. CNC Controller: Serving as the machine’s brain, the controller interprets G-code instructions, orchestrating precise movements and functions.
2. Column and Base: Providing structural support and vibration resistance, the column and base uphold the integrity of the machine during machining operations.
3. Knee and Saddle: These components enable vertical and horizontal adjustments of the workpiece, enhancing machining flexibility and precision.
4. Feed Mechanism: Housed within the knee, this electromechanical system governs vertical, longitudinal, and transverse feeds, dictating the cutting motion.
5. Work Table: The workpiece rests atop this platform during machining, offering a stable surface for precise operations.
6. Ram and Overhanging Arm: Specific to vertical and horizontal milling machines respectively, these components support the milling head, facilitating varied machining tasks.
7. Arbor Support: Essential for horizontal milling machines, the arbor support ensures stability and dampens vibrations during cutting operations.
8. Spindle and Tool Changer: The spindle drives the cutting tool while the tool changer enables seamless transitions between different tools, optimizing efficiency and productivity.
9. Milling Tool: These tools, tailored to specific machining operations, execute precise cuts based on programmed instructions, ensuring accuracy and quality.
10. Control Panel: Serving as the interface between the operator and the machine, the control panel enables seamless control and monitoring of operations.
CNC milling operates on the principle of converting CAD models into G-code instructions, guiding the machine through precise machining operations. This process involves securing the workpiece, executing programmed instructions, and monitoring feedback for accuracy.
The cost of a CNC milling machine is influenced by various factors, including:
From understanding the anatomy of CNC milling machines to delving into the intricacies of their operation and cost determinants, this article provides a comprehensive overview of CNC milling. With this knowledge, manufacturers can harness the power of CNC milling to achieve precision and efficiency in their machining endeavors.
Find various CNC-Machining products from our factory, and get the free OEM/ODM services.